Protect your investment by entrusting fixes and repairs to Euro Chill.
Euro Chill offers expert assistance for repairs for your medical refrigerators and freezers, which tirelessly maintain crucial items at precise temperatures.
They also offer elite servicing and maintenance to extend the lifespans, uphold efficiency and reduce the risk of refrigeration unit becoming compromised and inevitably lost.
Protect your investment by entrusting fixes and repairs to Euro Chill.
Euro Chill offers expert assistance for repairs for your medical refrigerators and freezers, which tirelessly maintain crucial items at precise temperatures.
They also offer elite servicing and maintenance to extend the lifespans, uphold efficiency and reduce the risk of refrigeration unit becoming compromised and inevitably lost.
What's included in a Euro Chill preventative maintenance service
Check installation of unit within guidelines
Clean under, behind, and around the fridge unit
Clean, and check the condenser
Check the piping for any damage
Check the evaporator for any icing
Check the drains are clear
Check the controller functions correctly
Clean the compressor and the surrounding area
Check the door seals for any damage, verify the seal condition
Check control panel and parameters
Check the refrigerator is adequate for the stock being carried
Check the probe is clear of product and situated in free air
Euro Chill service almost any type of equipment in our industry Australia-wide.
Servicing all brands and Australia-Wide.
Turn around time within one week for metro areas.
Quick and efficient turn around without compromising reliability.
Transparent, upfront pricing.
Flat-rate call out fee
$275 (incl gst)*
Servicing all brands and Australia-Wide.
Euro Chill service almost any type of equipment in our industry Australia-wide.
Quick and efficient turn around without compromising reliability.
Turn around time within one week for metro areas.
Flat-rate call out fee
$275 (incl gst)*
Transparent, upfront pricing.
What equipment can I service with Euro Chill?
Any medical refrigerator or freezer equipment can be serviced with us. Fill in the equipment details
information in the form and we will get back to you promptly regarding your request.


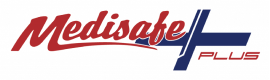
We can help service any medical fridge on the market.
What equipment can I service with Euro Chill?
Any medical refrigerator or freezer equipment can be serviced with us. Fill in the equipment details information in the form and we will get back to you promptly regarding your request.


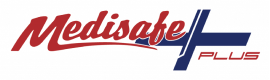
We can help service any medical fridge on the market.
Benefits of regular servicing
Maintains efficiency and extends the lifespan of your equipment by 20% on average.
Comply with National Vaccine Storage Guidelines recommendations.
Preventing problems before they turn into breakdowns.
Reduced risk of refrigeration unit becoming compromised resulting in loss of contents.
Benefits of regular servicing
Maintains efficiency and extends the lifespan of your equipment by 20% on average.
Comply with National Vaccine Storage Guidelines recommendations.
Preventing problems before they turn into breakdowns.
Reduced risk of refrigeration unit becoming compromised resulting in loss of contents.
We service Australasia-wide.
After lodging a service request, our expert technicians will travel to your premises to conduct an onsite inspection of your equipment at a time that suits you.
We service Australasia-wide.
After lodging a service request, our expert technicians will travel to your premises to conduct an onsite inspection of your equipment at a time that suits you.
The service requested above (Service) is subject to the terms below.
Timelines
The customer must acknowledge that repair, replacement and Service times provided are estimates only and may be varied.
Payment
The customer must make full payment for the Service upon completion of the Service and the provision of an invoice, unless otherwise agreed by Euro Chill. The customer acknowledges and agrees to pay a deposit for the Service, if requested by Euro Chill.
Euro Chill reserves the right to charge late payment fees, administration fees and legal costs for recovering overdue amounts. Euro Chill reserves the right to suspend or cancel scheduled Services if the customer has overdue amounts.
Service fee
*Euro Chill reserves the right to charge a $275 (inclusive of GST) Service call-out fee (such as for a technician to conduct an onsite inspection), including in the following circumstances:
- No fault was found at the time of inspection;
- The fault was user-related and not a defect, such as where the product has been improperly used or abused;
- The quote to repair is declined by the customer;
- Parts required to complete the repair are no longer available from the manufacturer and/or supplier;
- Service booking is canceled by the customer without at least 24hr notice;
- The customer fails to make themselves available, or, provide safe access to the property, at the time of the Service booking.